One of the advantages of starting an online workshop late, is having the benefit of the experience of the other participants. The Bowmont Fleece Challenge has generated some very interesting discussions in the Online Guild forum, and until now, I've been able to sit back, read, and take it all in.
Since my sample had to be shipped overseas from the UK, it was already washed. Even so, I found the discussion about washing fine fleece to be very informative. I was able to jump in with my fleece assessment, and preparing the fleece for spinning. Challenge participants tried a variety of preparation methods: hand carders, woolcombs, and spinning straight from the staple. One common problem was neps and trying to avoid them, which is not uncommon with fine fleece.
Since I am working with 50 grams, I decided not to experiment like I would if I had a whole fleece to play with. I want as little waste as possible! My plan was to use my favorite spinning tool, my dog comb, to open the locks. I would spin straight from these without further preparation.
What I discovered was that my regular dog comb was too coarse to comb the fine locks. So I decided to try what is called a "flea comb," also available in the pet department.
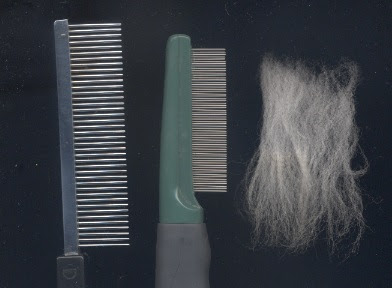
Then on to the spinning.

The first reason has to do with fiber length, as the longest fibers will draft out and spin first, leaving the shorter fibers behind to be spun last. This really isn't a factor with the Bowmont, as the quality of the fleece is consistent throughout the sample, no matter the fiber length, which varies very little anyway. It would be a factor if Bowmont was a dual coated fleece or had a lot of long guard hair. It would also be a factor if it was blended with another fiber of a different fiber length, for the same reason.
The second reason has to do with the physical structure of the individual fibers themselves. Wool fibers have microscopic scales. If you read my Angora rabbit posts, you probably remember me mentioning this then.
These scales are attached to the indivudual fibers like fish scales, the edges facing toward the tip. The fiber then can either be spun so as to smooth the scales down, or can be spun "against the grain" so to speak.
I must say that spinning them this way is wonderfully easy and smooth. The fiber has just enough lanolin left in it to make spinning a joy. Wanting to stretch my 50 grams as far as I can, I am spinning a finer yarn than I think I ever have before, except perhaps at a workshop.
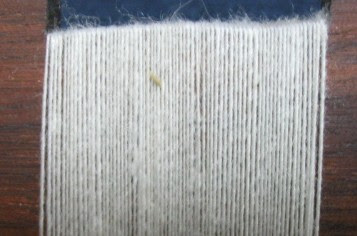

Next - A problem.
© 28 April 2007 at http://leighsfiberjournal.blogspot.com
Related Posts:
Bowmont Fleece 1 - The Breed
Bowmont Fleece 2 - Fiber Assessment
Bowmont Fleece 4 - A Problem
Bowmont Fleece 5 - A Comparison
Bowmont Fleece 6 - The Yarn