When it comes to calculating sett, I am a great fan of using charts. My favorite sett charts are found in the appendix of Peggy Osterkamp's New Guide to Weaving Volume 1: Winding a Warp and Using a Paddle. (You can see samples of these charts at her website, here.) Usually I can find what I need on one of these charts, however, I do have some oddball yarns that I've picked up here and there, which sometimes aren't listed.
Such is the case with the 16/3 cotton I want to use for my next multiple tabby weave experiment. So far, I've mostly used 8/2s cottons, because that's what I have a lot of. But I want to weave some everyday table napkins in navy and white, and I need a lighter weight warp yarn to go with the heavier navy weft.
Peggy's charts don't list 16/3 cotton, so I'm going to have to resort to another method to calculate the sett. I've decided to try something new, so here I am, thinking "out loud." Trying to explain concepts to others always helps clarify them for me. I only hope that in the end, all of this makes sense to you too!
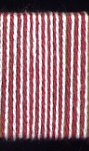
Wraps per inch (WPI) can be calculated in one of two ways. The first way is to physically wrap the yarn around a one inch measure and to count how many wraps it takes to achieve a solid inch of yarn. A more detailed description of how to do this is here.
The second way is by using the Ashenhurst Rule.
The Ashenhurst Rule calculates the wraps per inch without doing the wrapping. This is especially helpful for fine or slippery yarns. This method is found in Winding a Warp and Using a Paddle, on page 90. If you don't have that book and would like to read a more detailed explanation, you can find the excerpt here.
Here's the formula:
WPI = 0.9 x √ of YPP
WPI = wraps (diameters) per inch
√ = square root of
YPP = yards per pound

I considered doing a tutorial on how to use the McMorran Balance, but Laritza at Yorksett Arts & Crafts already has a good one, so I will refer you to it; just click here.
Using my McMorran Balance, I discover that the ypp is 5250. Grabbing my calculator and plugging that number into the formula, I get:
0.9 x √ of 5250 = 65.25 WPI.
Okay. So 65 and a quarter wraps will give me a solidly covered inch of my yarn. However, I need to make room for the weft, so that requires another calculation (this version also from Osterkamp):
Sett = WPI x weave firmness
This is how I learned to calculate sett.
WPI ÷ 2 = epi for balanced plain weave
WPI x 2/3 = epi for balanced 2/2 twill
Where WPI = wraps per inch and
..............epi = ends per inch
This gives what Peggy calls "maximum sett" for a balanced weave. If the sett is closer, then the fabric becomes warp dominant. One the other hand, the weaver may want a softer fabric. We have two choices here too. One can either weave a bunch of samples to decide what is best, or one can try ....
Allowing for the Purpose
This is something else found in Peggy's book. She lists suggested percentages to use depending upon the weave firmness wanted. This is based on the purpose for which the cloth will be used. You can find the box chart on page 93 of her book, or read the excerpt online here.
The threading draft I am planning to use is a broken twill, and my yarn is 65.25 WPI, so here are my calculations:
65 WPI x 2/3 (or .67 on my calculator) = 43 epi maximum sett
Taking Peggy's recommendation for 80% of maximum sett, (see "Sett: Making Your Weaving Easier").
43 x .8 = 34 epi to start.
So there you have it. The art and science of calculating sett. The science is in the math, and the art is in the weaver's choices based on knowledge and experience.
There are a couple of other methods, but these are the only ones I have experience with so far. I'd love to hear your thoughts and experiences, so please leave a comment if you feel so inclined.
© 26 May 2008 at http://leighsfiberjournal.blogspot.com
Related posts:
Another Way to Calculate Sett
Measuring Wraps Per Inch (WPI)
How to Use a McMorran Balance (Yorksett Arts & Crafts)