Enough of that and on to the fiber stuff.
Dan made it possible for me to attend the Southeastern Animal Fiber Fair (SAFF) over the weekend. It's been 2 years since I've been able to go so I was delighted to spend the day seeing old friends and immersing myself in all things fibery.
The drive to Asheville, NC was lovely. The weather was perfect and the autumn color, though just past peak, was still glorious.
This year's SAFF was the best I've seen. There were more vendors, more workshops, more demonstrations, more people, and less parking than before.

I would have liked to have taken Eileen Hallman's point spinning workshop, but our transportation situation prevented me from knowing whether or not I'd have a vehicle for the weekend. As it was, it was a last minute spontaneous decision to go anyway.
Here is the Beginning Spinning workshop.....
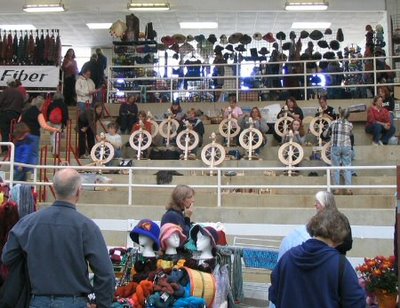
I went with a shopping list but didn't buy a lot. Typical for me, I got quite overwhelmed at all the beautiful fibers, yarns, tools, garments, projects, etc., and become exceptionally indecisive.
Some things I was looking for I found, other things I didn't. And I saw some things I wished I'd added to my list and planned on getting. I did buy more Cushings acid dyes and weaving bobbins. My luxury purchase was this......
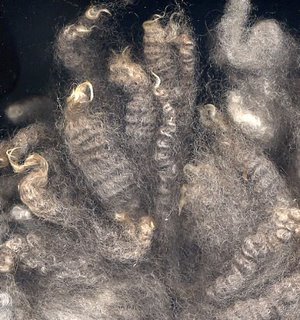
We also had a chance to visit the barns. My favorite (besides the angora bunnies who were all in the main arena) is this......
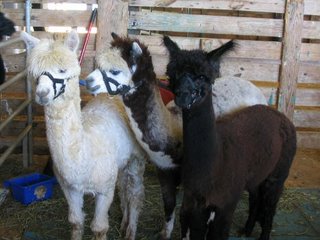
The best part of SAFF was getting to see friends. From the Blue Ridge Spinners I saw Carol, Mary, and Eva. From the Western North Carolina Fiber/Handweavers Guild I saw Betsy, Pat, and Charlene (though Mary and Eva are members of this too.) Betsy was my weaving teacher, so I was especially glad to visit with her. She is still just as encouraging as ever.
It's fun how an event like this can be so inspirational. It's refreshing as well as energizing. Now all I have to do is put that inspiration and energy to work.
© 2006 Leigh's Fiber Journal