In my last post I tried to give a simple explanation of the four basic twill categories. As promised, I'll now see how well I can do with a simple explanation of what advancing twills are.
Advancing twills could be categorized as "broken twills," (twills in which some shafts are skipped in the threading). In advancing twills, a number of warp ends are chosen (for example five ends) and are threaded as a section. Each section omits (skips) at least one shaft between it, and the next. (1,2,3,4,5 then 2,3,4,5,6 then 3,4,5,6,7 etc.) The result is that the warp section appear to be advancing (on paper that is.)
I understand things better with pictures, so let me try to explain it with some. Since advancing twills evidently are most suited for more than four shafts, my drawdowns will be for eight shafts.
A drawdown is a pen and paper (or computer if one has weaving software) representation of a weaving. The drawdown below is for an 8-shaft straight twill (each shaft threaded in successive order, 1 through 8). The threading is shown across the top, using numbers to keep track of which shaft is indicated.

The box in the upper right hand corner shows the tie-up. It indicates how the treadles are to be tied to the shafts, so that each treadle lifts whatever shafts are tied to it. In this case, I'm using a pretty standard 8-shaft twill tie-up. The end result will be that my weft will travel under three warp ends, over three, then under one, and over one. (This is known as a 3/3/1/1 tie-up.)
The column going down the right hand side of the page is the treadling order. Starting at the top, I treadle one through eight. Since this is the same as the threading pattern, it is also known as "as drawn in" or "tromp as writ."
The colored-in blue boxes give an idea of how the cloth will look once woven.
This whole thing is called a drawdown because one starts at the top corner (nearest the tie-up) and colors in the squares drawing down from the top.
OK. If I leave the tie-up and treadling the same, but begin to advance the threading, this is what I get:

The column going down the right hand side of the page is the treadling order. Starting at the top, I treadle one through eight. Since this is the same as the threading pattern, it is also known as "as drawn in" or "tromp as writ."
The colored-in blue boxes give an idea of how the cloth will look once woven.
This whole thing is called a drawdown because one starts at the top corner (nearest the tie-up) and colors in the squares drawing down from the top.
OK. If I leave the tie-up and treadling the same, but begin to advance the threading, this is what I get:

I've taken sections of five warp ends each, and advanced them by skipping (omitting) one shaft between each section. Pretty neat, huh?
So what happens if I change up the treadling?
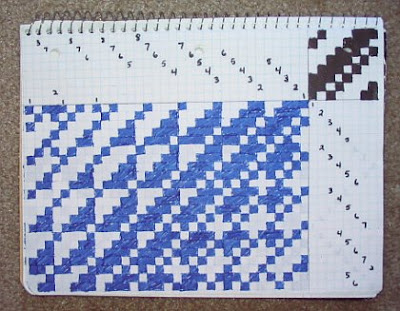
So what happens if I change up the treadling?
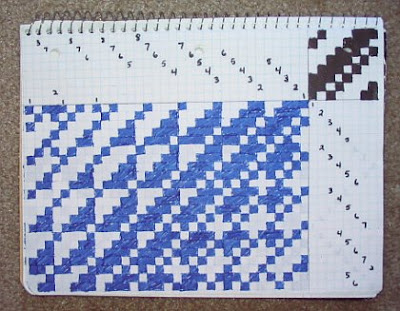
This one is treadled as drawn in. You can see that the treadling pattern is the same as the threading pattern.
What if I do a point-type treadling?

What if I do a point-type treadling?

As you can see, it is treadled one through eight and then reversed.
Of course, I only have a regular size graph paper notebook, so I only get a part of what the weaving will actually look like, but it's enough to really get me excited about this! And that's when I start asking, "what if........"
What would happen if I tried an extended point treadling? What if I did the advancing treadling and reversed each section? How would a rosepath treadling look? What if I used a different number of threads in my warp sections? How would it look if I changed the number of shafts skipped? And what about starting with a point twill threading to advance? Or an extended point threading? Then too, what if I changed the tie-up? Then there are color combinations to try. And different yarns to experiment with. As you can see, the possibilities are endless!
There are some rules to all of this, though at this point I don't have an experiential understanding of what they are. However, Stacey has done an excellent job with the workshop lessons, so that all the information is very handy.
My next step is to choose a yarn and measure a warp. I plan to warp the loom for the advancing draft above, and put on plenty of length to experiment with the treadling.
Related Posts:
Twills - The Basics
First Advancing Twill Samples
Advancing Twills - A Few More Samples
Continuing with Advancing Twill Samples
Advancing Twills - Second Verse
Of course, I only have a regular size graph paper notebook, so I only get a part of what the weaving will actually look like, but it's enough to really get me excited about this! And that's when I start asking, "what if........"
What would happen if I tried an extended point treadling? What if I did the advancing treadling and reversed each section? How would a rosepath treadling look? What if I used a different number of threads in my warp sections? How would it look if I changed the number of shafts skipped? And what about starting with a point twill threading to advance? Or an extended point threading? Then too, what if I changed the tie-up? Then there are color combinations to try. And different yarns to experiment with. As you can see, the possibilities are endless!
There are some rules to all of this, though at this point I don't have an experiential understanding of what they are. However, Stacey has done an excellent job with the workshop lessons, so that all the information is very handy.
My next step is to choose a yarn and measure a warp. I plan to warp the loom for the advancing draft above, and put on plenty of length to experiment with the treadling.
© 28 November 2007 at http://leighsfiberjournal.blogspot.com
Related Posts:
Twills - The Basics
First Advancing Twill Samples
Advancing Twills - A Few More Samples
Continuing with Advancing Twill Samples
Advancing Twills - Second Verse