That was my question when I first started spinning the Black Welsh roving from Judy. I toyed with the idea of spinning it as singles for weaving, but since I've been reluctant to jump into the waters of weaving with my own handspun, I thought perhaps it would be better to ply it. Needless to say, it has sat around on a bobbin for months. With another interesting spinning project imminent, I really needed that bobbin and so finally had to make a decision.
What I decided was to go ahead and ply it. I can still use it for weaving if I want, it will just make a chubbier weft. However, singles that aren't freshly plied and that sit around on bobbins for awhile, tend to temporarily set their twist. A single like this won't automatically try to balance itself when allowed to twist back on itself. Without that fresh energy, the question of how much plying twist to add becomes a challenge.
Here is what the single looked like when allowed to twist back on itself:
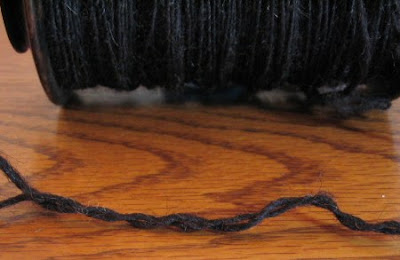
Looks too loose doesn't it? Of course, it often isn't possible to ply singles immediately after they are spun, so this is why I usually make a sample card. I not only attach a length of the single to the card, but also some freshly spun yarn plied back on itself. This tells me how my plying twist is required for a balanced 2-ply yarn. I also jot down any other information about the fiber: the breed, where it came from, fiber length, crimps per inch, wraps per inch, how I'm spinning it, etc. Unfortunately I lost or misplaced the sample card for the Black Welsh, and with it all that valuable information!
The thing to do was to re-energize the twist.
To do this I discarded several feet off the end of the bobbin. Then I broke off a short length and put it in a bowl of water.

The thing to do was to re-energize the twist.
To do this I discarded several feet off the end of the bobbin. Then I broke off a short length and put it in a bowl of water.

It didn't' take long before energy in the single "woke up" and started to twist back on itself. Now the twist was the same as when it was freshly spun. My challenge then, was try to ply so as to match my plying twist to the twist in this sample.


After I eyeballed a close enough match, it was simply a matter of counting treadles for the rest of the skein.
Here's what it looked like fresh off the niddy noddy:

Here's what it looked like fresh off the niddy noddy:
