A couple of posts ago, I showed you the toe-up sock toe that I really like. I've experimented with others but keep going back to that one. Not that I am exceptionally experienced when it comes to sock knitting. Off the top of my head I can recall about 17 or 18 pairs of socks that I've knit, but that's about it. I suppose that's enough pairs to settle on sock parts that one likes.
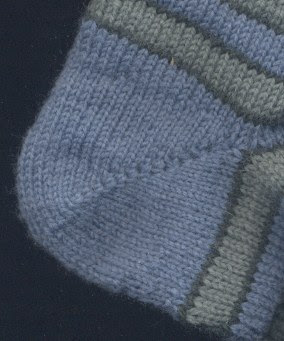
The reasons I've liked the short row heels is because they are the quickest and they use less yarn. I think they make a neat looking heel, as long as I keep the yarn snugged up as I do the wraps. Otherwise gaps develop. I have insisted to myself that these are decorative, but even so, I like a snug heel.
The biggest problem I've had with this heel is that gaps are left when knitting in the round resumes. This is usually eliminated by picking up an extra stitch or two on the first round after finishing the heel. I've been semi-successful with this, but it often looks a little sloppy to me. Of course, it might help if I could figure out whether to start the turn on a knit or purl row. No matter which I choose, it still doesn't seem to come out right, so perhaps it really doesn't matter (?) Another minus for this heel is that unless one uses a nylon reinforcing yarn in addition to the main yarn, it tends to wear out faster. But then there's the matter of getting a reinforcing yarn to match!
Heel flaps, on the other hand, take longer to knit and require more yarn. Usually these are knitted on cuff down socks, but can be used on toe-ups in a reverse fashion. One plus is that if one knits it with slip one, knit one (or easier yet, Lucy Neatby's slip one, purl one), the yarn carried across the slipped stitches creates a sturdier heel.
My problem with these heels stems from the fact that no matter what I do, my knit and purl tensions are never the same. This results in a rather trapezoidal shaped flap, instead of a nice neat square one. I can't say that this effects the fit of the sock noticeably, but it still bugs me. Oh, and I've managed to get a gap with this heel as well.
Before I conclude, I think that I should admit that I've never tried an "afterthought heel." For some reason I'm a little leery of this heel, though I don't know why. I suppose that I should be brave sometime and give it a try just to see what it's like. Of course, knowing me, I'll have to give it three or four tries before I get the hang of it, and I'm not sure that I want three or four more pairs of socks with goofy looking heels.
Perhaps I should have named this post "In Search of the Perfect Sock Heel." I know that I certainly haven't found it. Has anyone? Does such a thing even exist? I'm open to suggestions.